Application of Seals
- Construction Machinery
- Mining Technology
- Industrial Equipment
- Oil And Gas Industry
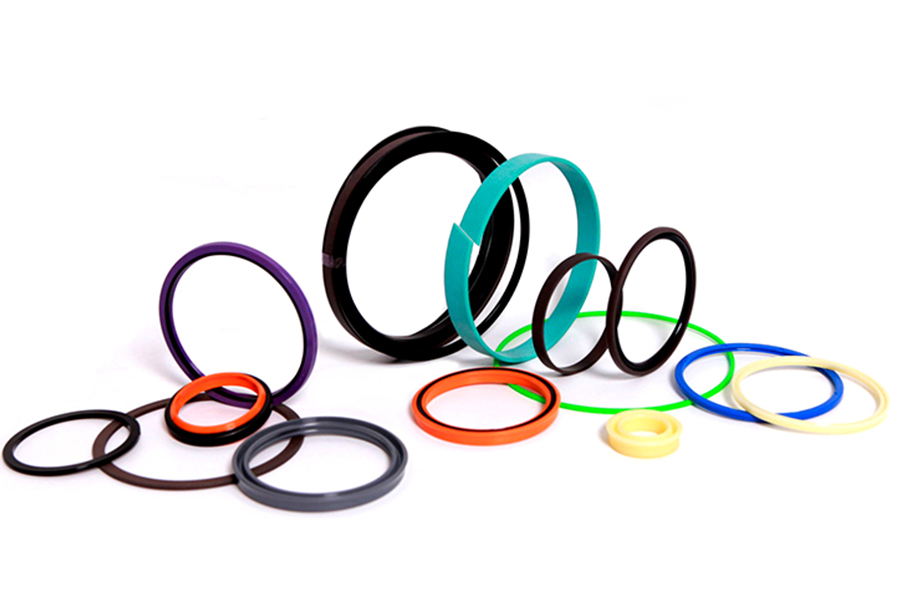
- Construction Machinery
- Mining Technology
- Industrial Equipment
- Oil And Gas Industry
Construction Machinery
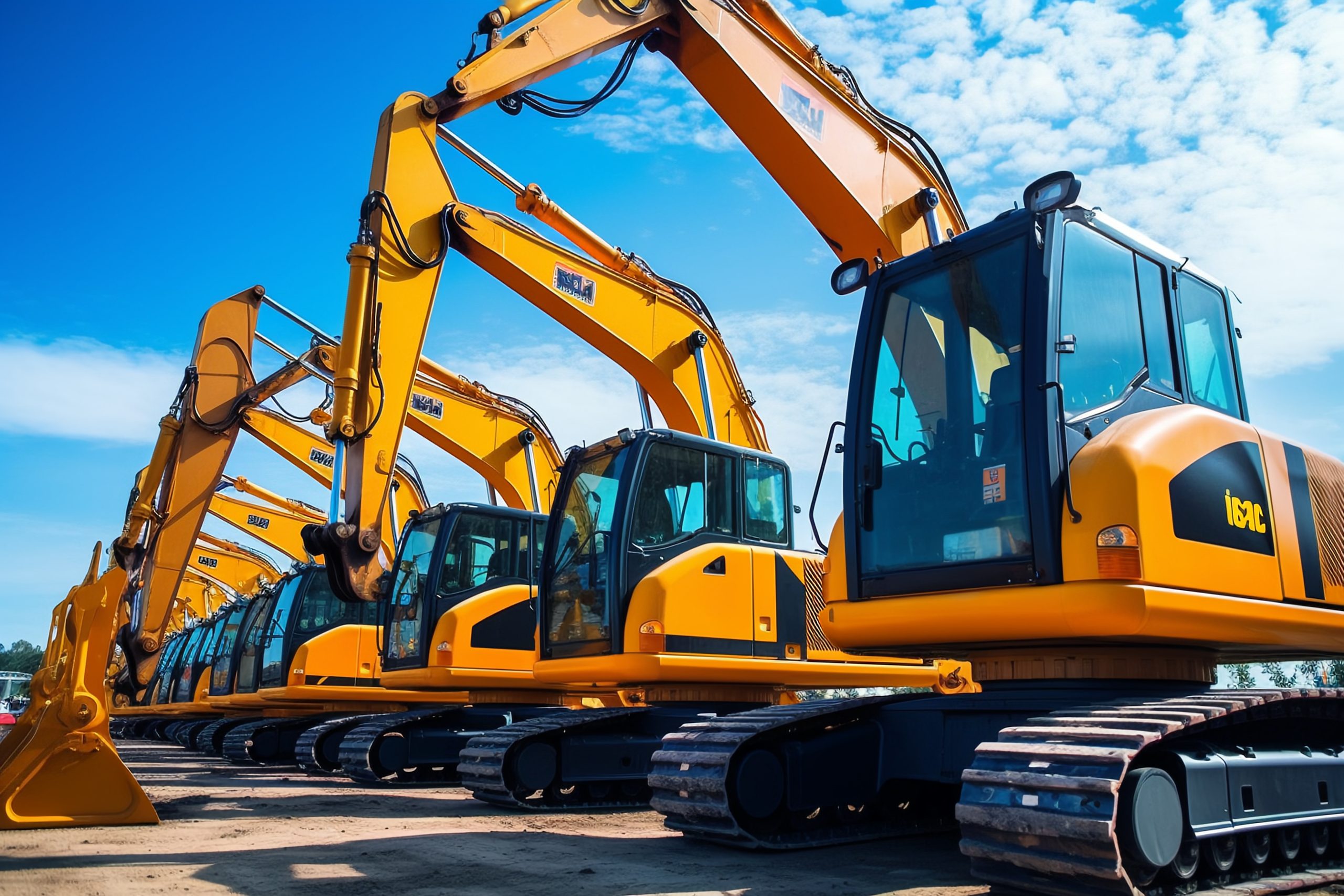
Cylinders are vital in construction machinery, and their applications are wide and diverse. As the power component of the working device, the cylinder can be used as the power component of equipment such as the loader boom and the bucket cylinder, and the hydraulic energy is converted into mechanical energy to achieve efficient motion control of the equipment. Therefore, maintaining the excavator cylinder is very important, as it can effectively extend its service life and improve work efficiency. Regularly check the seals inside the cylinder (such as rubber seals, dust covers, etc.). If they are found to be damaged or aged, they should be replaced in time to ensure the normal operation of the cylinder.
The role of seals in construction machinery is mainly reflected in the following aspects:
- Prevent leakage: The main function of the seal is to prevent the leakage of liquids (such as hydraulic oil) in construction machinery and ensure the normal operation and efficiency of the machine. This is essential for improving the volumetric efficiency and mechanical efficiency of the machine.
- Prevent pollution: The seal can prevent external contaminants from entering the machine and protect the inside of the machine from dust, moisture, and other impurities. This is very important for keeping the inside of the machine clean and extending the life of the machine.
- Improve machine efficiency: By reducing internal leakage, external leakage, and penetration, seals help improve the efficiency of construction machinery. For example, reducing friction losses can improve the mechanical efficiency of the machine.
Protect mechanical parts: Seals can protect mechanical parts from corrosion and wear, extending the service life of the parts.
Maintain pressure: In hydraulic systems, seals can maintain the required working pressure to ensure the effective operation of the system.
Reduce energy consumption: Compared with traditional stuffing box seals, mechanical seals consume less energy.
Adapt to extreme conditions: Mechanical seals can work under high pressure and extreme temperatures to maintain their sealing effect.
Reduce maintenance requirements: Due to the design and use of high-quality materials, mechanical seals have less wear, reducing the need for frequent maintenance and ensuring higher machine reliability.
The composition of engineering cylinder seals mainly includes the following types:
- Wiper Seal: installed outside the hydraulic cylinder end cover to prevent external contaminants from entering the cylinder. According to the installation method, dust rings can be divided into snap-in and press-in types. Snap-in dust rings are more common, usually stuck in the groove on the inner wall of the end cover, and are suitable for less harsh environmental conditions. The material is usually polyurethane with case, NBR etc.
- Rod Seal: Also known as a U-cup, it is the main piston rod seal installed on the inside of the hydraulic cylinder end cover to prevent hydraulic oil leakage. The piston rod seal is made of polyurethane or NBR. In some cases, it needs to be used with a support ring (also called a retaining ring) to prevent the seal from being squeezed and deformed under pressure.
- Buffer Seal: As an auxiliary piston rod seal, it is used to protect the piston rod when the system pressure suddenly increases, to prevent seal extrusion, and to allow the seal to withstand higher pressure.
- Guide Ring: Installed on the hydraulic cylinder end cover and piston, it is used to support the piston rod and piston, guide the piston to move linearly and prevent metal-to-metal contact. The materials include nylon, phenolic resin cotton fabric, bronze coated with PTFE, etc.
- Piston Seal: It is used to isolate the two chambers of the hydraulic cylinder and is the main seal in the hydraulic cylinder. It is usually a two-piece type, with an outer ring made of PTFE or nylon and an inner ring made of NBR rubber. There are also many variations, including bronze coated with PTFE
In summary, seals play a vital role in construction machinery. They not only protect the machine from the external environment but also improve the efficiency and reliability of the machine.
Mining Technology
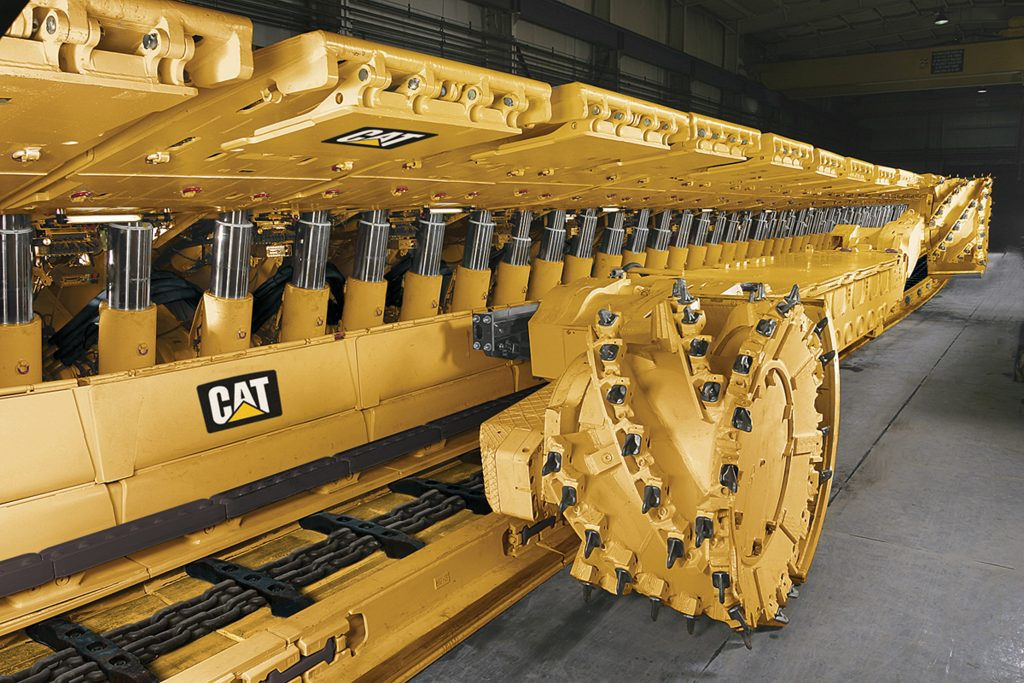
In mining equipment, especially in longwall mining, a “longwall proof support seal” is a key component to ensure equipment performance and safety.
The following are the roles and applications of seals in longwall support systems:
- Prevent hydraulic oil leakage: Seals in longwall support systems are used to prevent hydraulic oil leakage, which is essential to maintain the stability and efficiency of the support system. Leakage not only leads to reduced efficiency but may also cause safety accidents.
- Wiper Seal: Seals can prevent dust and moisture from entering the support system, protect internal components from corrosion and wear, and extend the life of the equipment.
- Adapt to extreme conditions: Longwall support systems may work under extreme conditions, such as high temperature, high pressure, and chemical corrosion environments. Seals must be able to adapt to these conditions to maintain the normal operation of the equipment.
- Improve automation efficiency: In longwall support systems, seals help achieve 100% automated operation, and improve production efficiency and safety.
- Customized design: The seals of longwall support systems can be customized according to specific application requirements to meet the specific conditions of different coal mines, such as coal seams of different thicknesses, unstable roofs, and geological faults.
- Maintenance and repair: Seal replacement is an important part of the maintenance and repair process of the longwall support system. Professional technicians will inspect, test, and replace damaged seals to ensure the reliability and cost-effectiveness of the system.
- 7Improve system stability: Seals help improve the stability of the longwall support system and reduce failures and downtime caused by poor sealing.
In summary, seals play a vital role in the longwall support system. They not only protect the equipment from the external environment but also improve the efficiency and safety of the system.
The types of mine hydraulic support seals mainly include the following:
- Dust seals: used to prevent dust and contaminants from entering the hydraulic system and protect internal components from contamination.
- Rod seals: used to seal the piston rod of the hydraulic cylinder to prevent hydraulic oil leakage.
Static seals: seals used in fixed or static positions.
- Guide Ring: used to guide the linear motion of the piston rod, reduce friction and wear,
- Piston seal: used to seal the piston of the hydraulic cylinder to prevent the hydraulic oil from leaking from one chamber to another.
- Bud-shaped seal ring: This is a piston rod seal, which is composed of an O-shaped seal ring made of synthetic rubber and a Y-shaped seal ring made of cloth-reinforced rubber.
- Drum-shaped seal ring: used to seal the piston, most of the materials are rubber, and some seal rings have been made of polyurethane in recent years.
- Combined seal ring: a separate outer ring is composed of a material with a small sliding friction coefficient and high wear resistance, a separate inner ring is composed of a material with good elasticity, and a separate retaining ring is composed of a material with high strength and wear resistance. The three can be separated and combined to form a sealing structure.
- Polyurethane monomer seal ring: a monomer seal ring made of polyurethane material, and a sealing structure that can automatically compensate for the sealing gap is adopted.
These seals work together to ensure the normal operation and efficient work of the hydraulic support. Each seal has its specific function and application scenario, which is essential for maintaining the stability of the hydraulic system and extending the life of the equipment.
Industrial Equipment
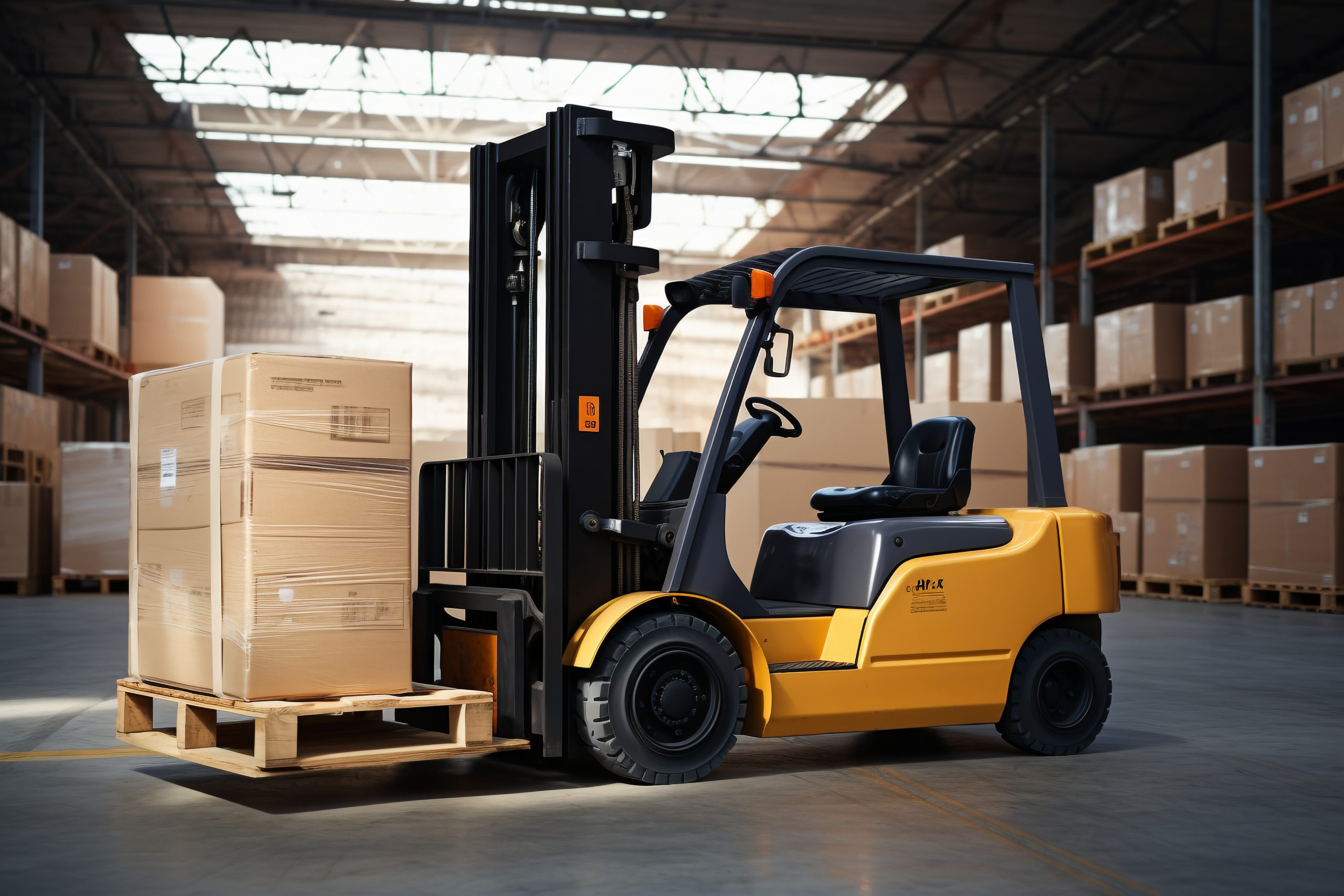
In addition to engineering machinery and mining equipment, seals are mostly used in industrial equipment to ensure the safe and efficient operation of industrial equipment. It involves preventing liquids, gases dust, and other media from leaking from the inside of the equipment or preventing external pollutants from entering the inside of the equipment.
Main types of industrial seals
Static seals: The seal is relatively stationary with the joint surface, commonly seen in seals between fixed parts, such as rubber O-rings, gasket seals, and sealants.
Dynamic seals: The seal moves relative to the joint surface, commonly seen in seals between moving parts, such as mechanical seals, oil seals, and packing seals.
Some main application areas of industrial seals:
Automotive industry: In automobile engines, transmission systems, and braking systems, rubber seals are widely used, such as piston sealing rings, shaft seals, etc., to ensure the sealing performance and reliability of various parts of the car.
Aerospace: Rubber seals undertake key tasks in the seals of aircraft engines, fuel tank seals, etc., to ensure flight safety and performance.
Petrochemical: Seals prevent fluid leakage in pipelines, valves, pumps, and other equipment in the petrochemical industry to ensure the smooth and safe operation of equipment.
Coal chemical industry: In the coal chemical industry, seals are used to prevent gas or liquid leakage and ensure the safety of the production process.
Metallurgy: In the metallurgical industry, seals are used to seal equipment in high-temperature and high-pressure environments to prevent molten metal leakage.
Textile: In textile machinery, seals are used to prevent lubricating oil leakage and fiber dust intrusion, and protect mechanical parts.
Electricity: In transformers and switchgear in the power industry, seals are used to protect electrical equipment from moisture and dust intrusion to ensure the normal operation of equipment.
Machinery, chemical industry, energy, and other fields: Silicone seals ensure the normal operation and stability of mechanical equipment in hydraulic systems, pneumatic systems, pump seals, valve seals, etc.
These application areas show the versatility and importance of seals in modern industry. They play a key role in ensuring equipment performance and improving safety and environmental protection.
Oil And Gas Industry
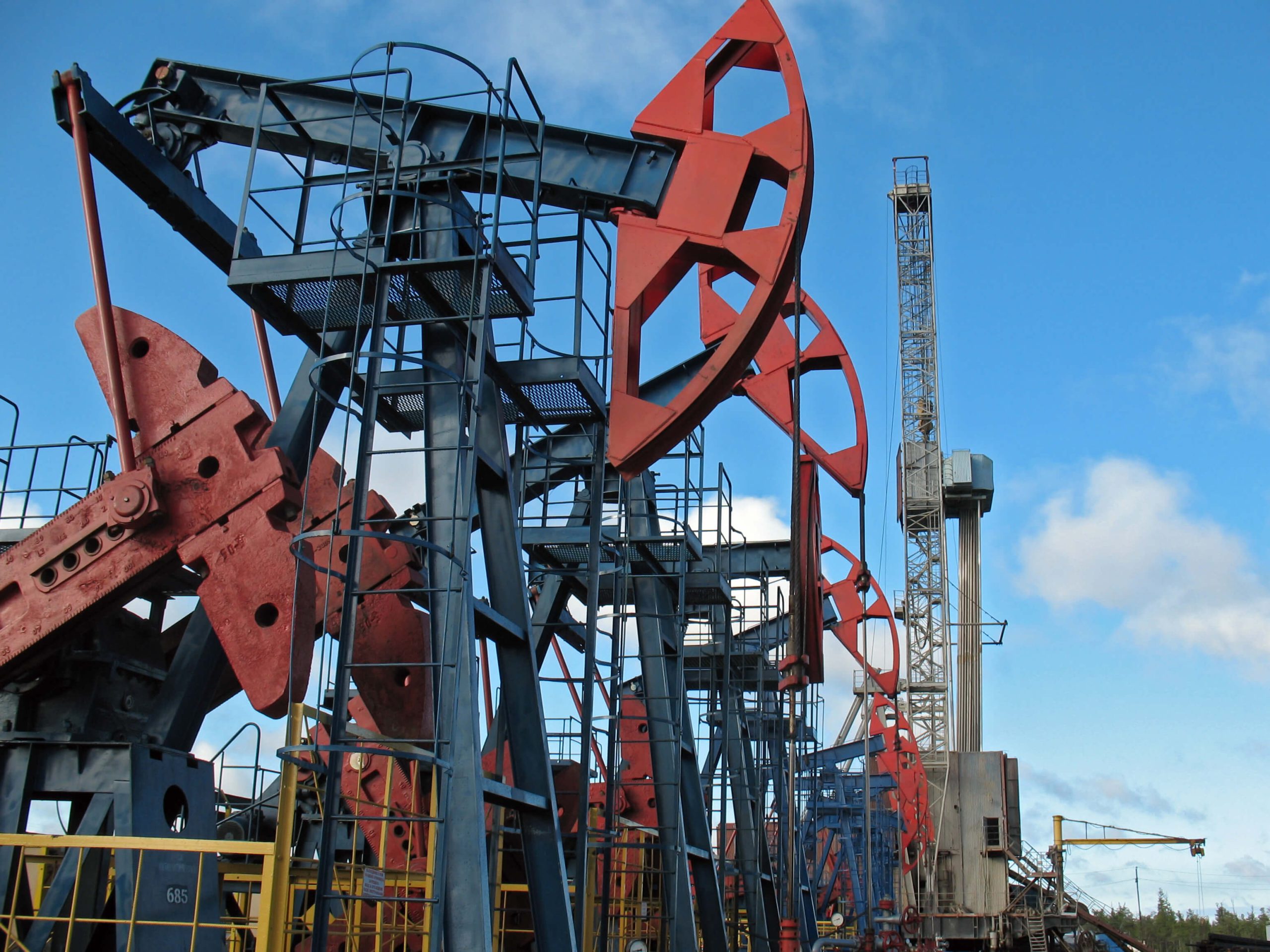
Oil and gas sealing technology is mainly used in the oil and gas industry.
The following are some key application areas and features:
Oil and gas extraction and transportation: Oil and gas sealing technology is used in oil and gas field extraction, oil and gas pipelines, and related oil and gas processing equipment to ensure the sealing of each link from oil and gas field extraction to oil and gas transportation to prevent oil and gas leakage.
Oil refining and chemical industry: In the field of petrochemical industry, oil and gas sealing technology is used in a variety of chemical equipment such as ethylene cracking, polyolefins, EOEG, aromatics, PTA, PET, caprolactam, as well as compressors, agitators, key pumps and other dynamic equipment.
Mechanical seal: Oil and gas sealing technology has been studied and applied for a long time in the mechanical seals of core dynamic equipment such as ethylene three machines, reactor circulation pumps, high-speed liquid ammonia pumps, and PTA oxidation kettle agitators, and has accumulated in-depth and comprehensive application experience.
Dry gas seals and control systems: Zhongmi Holdings provides customers with a full range of mechanical seals, dry gas seals, and control system products to provide guarantees for the stable operation of dynamic equipment.
Special material seals: In response to the special needs of the oil and gas industry, seals made of various materials have been developed, such as fluoro rubber, polytetrafluoroethylene and its composites, plastics, etc. These materials have the characteristics of high-temperature resistance, high-pressure resistance, chemical medium compatibility, etc.
Subsea equipment seals: Oil and gas sealing technology is also used in equipment such as submarine ball valves, gate valves, throttle valves, multiphase flow meters, as well as submarine wellheads and Christmas tree equipment that meet API standards.
High-performance seal research and development: PetroChina’s independently developed high-performance oilfield seals have broken the dependence on imports. These seals have undergone rigorous 70MPa-rated limit pressure tests at Baoshi Machinery and have excellent performance.
Chemical compatibility of sealing materials: There are many types of liquids that need to be controlled in the petrochemical and natural gas industries, such as aromatics, rust inhibitors, acid gas, drilling fluids, seawater, carbon dioxide, hydrogen sulfide, etc. These media are often mixed together and have the characteristics of high temperature and high pressure, so the sealing materials used are required to have excellent quality and good chemical compatibility.
Oil and gas sealing technology is one of the key technologies to ensure the safe, efficient, and environmentally friendly operation of equipment in the oil and gas industry. Through continuous technological innovation and material research and development, the application areas of oil and gas sealing technology are constantly expanding and the performance is constantly improving.